- Article
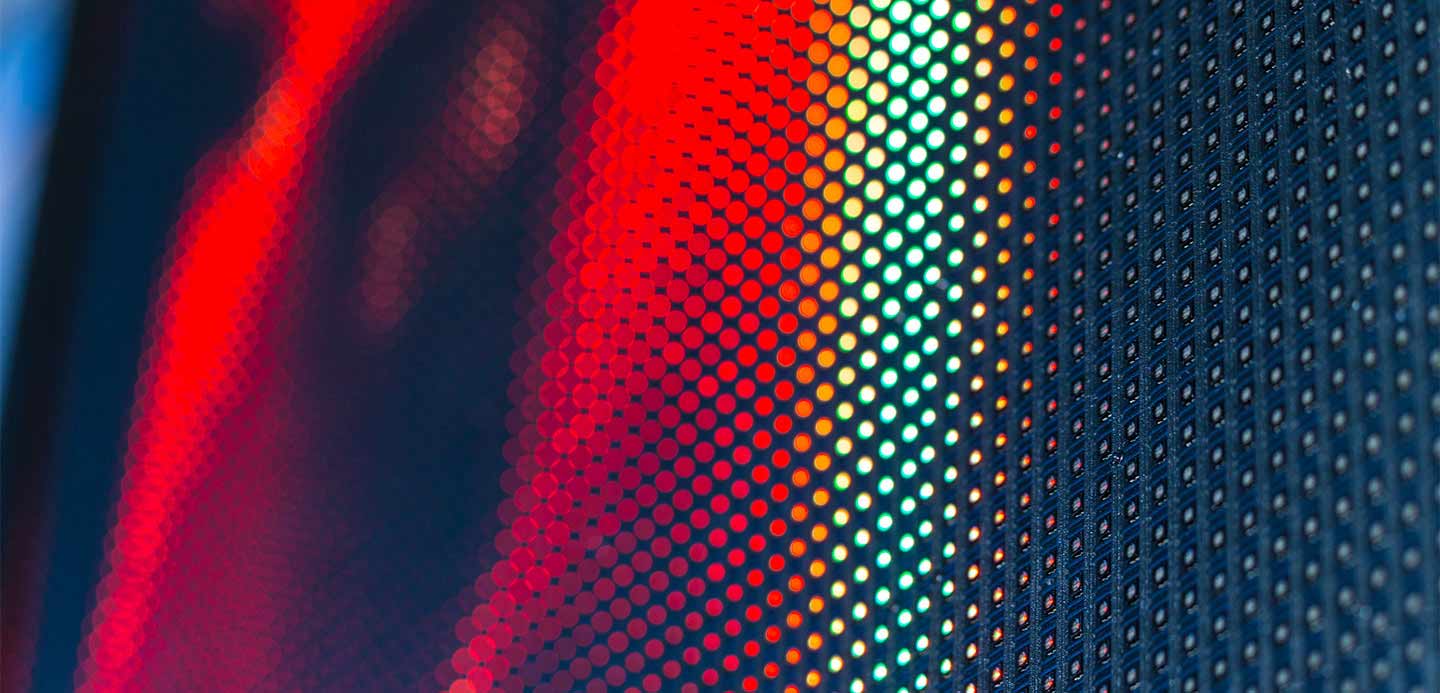
- Innovation & Transformation
- The Future of Infrastructure
Behind the scenes of semiconductors
The rise of advanced technology is making semiconductors more important than ever, and Asia Pacific is at the heart of this strategically important industry. As the chip sector evolves, businesses will need to be prepared for changes resulting from technological progress and the realignment of global supply chains.
Behind every digital disruption is a hardware foundation. Microchips, which combine multiple semiconductor components to control a range of electronic processes, have been driving innovation since Texas Instruments developed the world’s first commercialised integrated circuit (IC) in the 1950s. Since then, chips have become ever smaller and more powerful, making the technology a core component of everyday appliances, and manufacturing has migrated across the Pacific, creating a complex global value chain.
Today, demand for advanced chips is surging as businesses seek to apply artificial intelligence (AI) technology to unlock a new wave of innovation. At the same time, tensions in global supply chains are continuing to exert pressure on the sector. Global sales of chips are expected to almost double in the decade from 2023, reaching USD1.2 trillion by 2033, according to a recent forecast by Spherical Insights.1 Virtual reality, gaming, autonomous driving and advances in telecommunications will fuel rapid growth, analysts say.2
As the next generation of digital disruption dawns, businesses in Asia Pacific will need to keep a keen eye on developments to capitalise on new opportunities and shore up their supply chains in a rapidly evolving landscape.
Understanding semiconductors
Semiconductor chips are wafer-thin fabrications that integrate multiple electronic transistors, resistors and capacitors all on a single, conductive substrate.
Previously, components were individually produced, arranged on a foundation, and wired together. The more transistors an application needed, the bulkier a device would get, which ultimately made circuitry slow as current travelled across greater physical lengths.
ICs, or microchips, solved both the size and wiring challenges, combining all components into a single package forged from one material – typically silicon.
While American and European firms continue to dominate in design of high-end chips and the most advanced manufacturing equipment (Taiwan’s MediaTek and RealTek are the only non-US fabless companies among the global top 10),3 they outsource the actual manufacturing to other companies, known as fabs or foundries.
Taiwan Semiconductor Manufacturing Co is a so-called pure play foundry and does little else, but it controls more than half the global market for manufacturing of the most advanced semiconductors. South Korea’s Samsung Electronics designs and makes its own chips but also controls more than 10% of the global foundry market; local rival SK Hynix is the world’s second-biggest memory chipmaker as well as having an expanding contract fab business.4
While almost all electronic devices today need chips, not all of them need the latest and most advanced versions. That leaves a vast hinterland of chip production that has come to be dominated by Asian manufacturers, including Taiwan’s UMC and PSMC and China’s SMIC and Huahong Group.5
Now found in consumer electronics, transport, banking and healthcare systems, chips permeate daily life through countless applications from fitness trackers to automobiles, washing machines and mobile phones.
With each new area of digital transformation, semiconductors only become more essential for businesses. The booming electronic commerce and digital payments in Asia Pacific are only possible thanks to advances in processing power.
Demand for more advanced processing is also transforming the chip sector, as customers look for specialised hardware to support new technology, including AI.
Complex manufacturing processes
Changes in the chip sector do not happen overnight. The intricacies of semiconductor production, from the post-design stage to packaging, can take up to four months involving hundreds of steps, including oxidation, photolithography, and etching.6
Building a fabrication plant can take four years or more to complete and cost billions of dollars. A new Samsung Electronics fab in Texas is expected to cost over USD25 billion.7
Fabrication equipment alone demands a staggering investment. Extreme ultraviolet lithography machines need hundreds of engineers to install and command a commercial price near USD400 million.8
Japan lies third behind South Korea and Taiwan in global chip production, but accounts for more than half of the semiconductor material production market and around a third of the equipment-production market. Companies such as Tokyo Electron and Nikon excel in producing cutting-edge micro-lithography tools and other equipment; Shin-Etsu is a supplier of raw materials such as silicon wafers.9
Once a fab is up and running, workers follow stringent cleanliness standards, wearing "bunny suits" and undergoing filtered air showers to maintain an environment 10,000 times cleaner than the outside air.10 The tiniest defects, even a speck of dust, can compromise a microchip, emphasizing the critical nature of quality control, and failure risk, in semiconductor manufacturing.
Malaysia has developed a globally significant niche in testing and advanced packaging – an area of growing importance as individual chips reach capacity constraints. Bundling together chips during the packaging process is emerging as a way to sidestep the limits of physics, especially in AI and virtual reality applications.11
SK Hynix and TSMC in April announced a tie-up to produce next-generation memory chips enhanced with advanced packaging techniques “to break memory performance limits for AI applications”.12
Innovation for the future
The semiconductor industry is in a continuous arms race of innovation where seemingly small advances can prompt substantial market share gains. Efforts to reduce component sizes that are already measured in nanometres, with companies like Intel, Samsung, and TSMC competing to ship the first 2-nm chip.13
Global interest in generative AI is accelerating competition and product development even more. While chip giants like AMD and Intel are fiercely competing with Nvidia to release newer, more efficient, and more powerful AI chips,14 names more often associated with software, such as Google or Microsoft are also entering the AI chip race, as are social network Meta and e-commerce giant Amazon.15
The industry is adapting to new dynamics too, fuelled by efforts to de-risk supply chains. Sustainable manufacturing initiatives, incorporating green chemistry solutions and improving water efficiency are also becoming more important to the industry, highlighting a potential growth area of opportunity as the world transitions to a more resource-efficient and low-carbon economy.16
Just as the use of silicon in chip manufacturing processes powered the computer era, a new evolution in materials may be about to shift the landscape again. New developments in compound semiconductors — using a blend of materials such as gallium nitride or silicon carbide — offer enhanced performance for unique functionalities, such as boosting 5G and 6G bandwidths for telecommunications or vertical-cavity surface-emitting lasers (VCSEL) used in 3D sensing for autonomous vehicles.17
Maintaining a stable supply of sophisticated chips will be crucial for industries looking to harness the power of advanced technology. Self-driving cars, for example, require over 3,000 semiconductors to operate without driver input.
Chips will also play a fundamental role in the green transition, enabling clean energy technologies such as solar panels, wind turbines, and energy-efficient lighting.
Semiconductors are only becoming more integral to our digitally connected world. An understanding of this complex sector’s evolution can help businesses in Asia Pacific ensure they are prepared for the risks and opportunities that the future holds.